Orbital Welding
Vishes Global stands tall as a supplier of best available technology to solve a set of challenges faced by the stainless-steel industry such as cleaning and corrosion. We employ such technologies which encompass nontoxic passivation chemicals, sophisticated portable and fixed electro-polishing systems, stainless steel test kits and environmentally safe sanitary cleaners.
Incorporating these technologies enables our clients to attain optimal results and superior quality finishes for stainless steel throughout every stage of the fabrication process, from initial construction to installation and ongoing maintenance of these crucial assets. We strictly adhere to the ISO 14000 AND ISO 18000 quality systems and are a proud channel partner of Nikit Engineers for PAN India products.
Profile Welder:
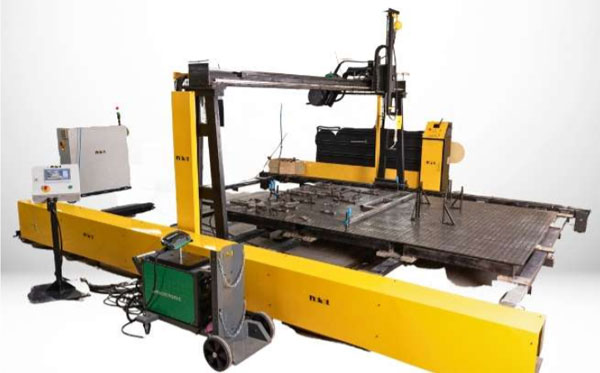
A Profile Welder is a type of welding machine that is specifically designed for soldering
profiles or sections of metal. It is commonly used in industries such as construction,
automotive and manufacturing, where joining metal profiles is a frequent requirement.
These machines are typically equipped with specialized fixtures and clamping mechanisms
that secure the metal profiles in place during the welding process. This ensures precise
alignment and stability, resulting in strong and accurate welds and joints.
Various types of welding techniques can be used with a profile welder such as MIG (Metal
Inert Gas) welding, TIG (Tungsten Inert Gas) welding or even laser welding, depending on
the specific application and requirements.
These machines often offer adjustable settings for controlling parameters such as heat
intensity, welding speed and penetration depth, allowing for flexibility and customization
based on the type and thickness of the profiles being welded. Profile welders play a crucial role in the fabrication of metal structures such as frames, trusses and supports as well as in the assembly of automotive components, architectural elements and other similar applications.
Advantages of Profile Welders:
• Efficient and precise welding: The said apparatus are equipped with specialized fixtures and clamping mechanisms that ensure precise alignment of the metal profiles. This enables accurate and consistent welds, reducing the need for rework and improving overall welding efficiency.
• Versatility: These machines can be used with various welding techniques such as
MIG, TIG or laser welding, making them versatile machines that can adapt to
different soldering requirements and materials.
• Increased productivity: With the ability to weld multiple sections of metal together
simultaneously, such sort of devices can significantly increase productivity
compared to manual welding methods. This allows for faster production cycles and
shorter lead times.
• Strong and durable welds: These instruments provide a high-quality welding
process, resulting in strong and durable joints. The precise alignment and controlled
parameters ensure optimal penetration and fusion, resulting in welds that can
withstand heavy loads and stress.
• Consistency and repeatability: These mechanisms offer consistent and repeatable
soldering results. The machines are programmed with specific parameters, ensuring
that each weld produced is consistent in terms of quality and appearance. This is
especially important in industries with strict quality control standards.
• Improved safety: These engines are designed with safety features such as
enclosures, shields and sensors that protect the operator from arc flash, sparks and
harmful fumes. Additionally, the use of automated welding reduces the risk of
human error and the associated safety hazards.
• Cost savings: Although the initial investment in a profile welder may be higher than traditional manual welding methods, the increased productivity, reduced rework
and consistent weld quality can result in long-term cost savings. Additionally,
automated soldering reduces labor costs and minimizes material waste.
Features and Techniques of Orbital Welders:
• Uranami Weld Bead: This type of weld bead pattern is often desired for aesthetic
purposes or to enhance certain mechanical properties of the weld such as fatigue
resistance. Achieving a uranium weld bead pattern typically involves specific
welding techniques and parameters which can be implemented using this
equipment.
• AVC (Auto Voltage Controller): AVC or Auto Voltage Controller is a feature found in
some orbital welding systems. It is designed to maintain a consistent arc length by
automatically adjusting the voltage during welding. This feature is crucial for
ensuring consistent weld quality especially when dealing with variations in material
thickness.
• Weaving: Weaving technique refers to where the weld torch or electrode is
oscillated from side to side during the welding process. This motion creates a wider
weld bead and helps ensure proper fusion between the base metals. Weaving is
commonly used in orbital welding especially for welding thicker materials or when
additional weld reinforcement is required.
Profile Welders Application industries:
• Manufacturing of metal structures: These type of devices are commonly used in
the manufacturing of metal structures such as frames, trusses, supports and ladders
by welding different sections of metal together to create a solid structure.
• Automotive industry: These tools are used to assemble various automotive
components such as chassis, exhaust systems, frames, roll cages and suspension
systems.
• Construction industry: Such type of welders are widely used in the construction
industry to fabricate metal structures for buildings, bridges, tunnels and other
infrastructure projects.
• Shipbuilding: These specific devices are widely used in the shipbuilding industry,
where they play a crucial role in welding multiple sections of metal together to
create a sturdy ship structure.
• Furniture manufacturing: These equipment are used in furniture manufacturing to
create metal chairs, tables and other metal furniture.
• Railways: These machines are used in the railway industry to create train tracks,
railway platforms and overhead electrification systems.
• Aerospace industry: The aforementioned appliances are used to fabricate metal
structures such as spaceship frames, fuselage and engine casings, used in the
aerospace industry.